Photovoltaic hot-dip galvanized reinforced plate application

hot dip Galvanized ReinFoRCinG Steel FoR ConCRete
the practice of hot dip galvanizing steel reinforcement in concrete is now a well-proven safeguard against corrosion. The maxim that "prevention is better than cure" finds no greater example

(PDF) Guideline for Hot-Dip Galvanised Components in Steel and
PDF | On Jan 1, 2017, Dieter Ungermann and others published Guideline for Hot-Dip Galvanised Components in Steel and Composite Bridge Constructions | Find, read and cite all the research

Galvanized reinforcement in concrete structures
Hot dip galvanizing is the most common method of galvanizing and is that which should always be specified for the coating of structural steels including reinforcing bar. The coating produced by

Hot-Dip Galvanized Reinforcing Steel: A Concrete Investment
better. This allows the same reinforced con-crete design specifications (bar size, lap lengths, etc.) to be used for galvanized rebar as unprotected rebar. 3 Straight lengths of galvanized rebar

Hot dip galvanizing – Process, applications, properties
by galvanizing, electroplating, mechanical plating, sherardising, painting with zinc-rich coatings and zinc spraying or metallising. Of these the galvanizing process is by far the most widely

Hot-Dip Galvanized Reinforcing Steel A Construction Perspective
Discuss the hot-dip galvanizing process • Identify reasons specifiers choose hot-dipped galvanized (HDG) reinforcing steel (corrosion protection, durability, longevity, availability,

Suggested Specification for Hot-Dip Galvanizing Reinforcing Steel
for Hot-Dip Galvanizing . Reinforcing Steel . Revised February 2002 This suggested specification is provided as a guide to producing a quality document calling for hot-dip galvanizing of

Galvanized Steel Empowering Renewable Energy Sustainability
Hot-dip galvanized steel can last between 20 and 100 years before galvanized reinforcing steel can be found in ASTM A767 and ASTM A1094. Further of galvanized steel in this application

Hot DIP Galvanized Steel+ Aluminum Magnesium Zinc Plate+ Pre Galvanized
Production name: Hot dip galvanized steel+ aluminum magnesium zinc plate+ pre galvanized solar single row tracking bracket Our self-developed independent single-row tracking bracket

Galvanized coatings for buildings and structural steel
Galvanized steel is often used in conjunction with timber in structural steel and as components (bolts, nails, plates, etc). When galvanized steel products and fasteners are installed in direct

The Protection of Structural Steel by Hot-dip
EN ISO 1461: Hot dip galvanized coatings on fabricated iron and steel articles-Specifications and test methods and EN ISO 14713 Protection against corrosion of iron and steel in structures-Zinc
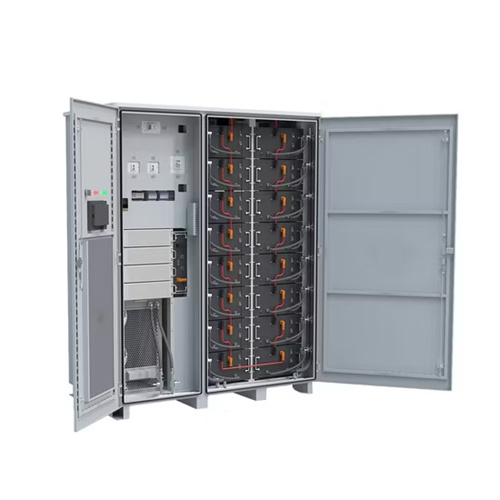
6 FAQs about [Photovoltaic hot-dip galvanized reinforced plate application]
Does hot dip galvanizing protect against corrosion?
Selected case studies where hot dip galvanizing has been used in wind, solar, hydropower and biofuel applications globally will be described. The attributes of hot dip galvanizing that favored the selection of hot dip galvanizing over other corrosion protection schemes in these cases will be described.
What is hot dipped galvanization?
As a process point of view, in case of hot dipped galvanization, once the structural member is completely fabricated including welding, punching, drilling, cutting etc. all operation, it is immersed into molten zinc and kept for requisite time duration. This ensures complete zinc coverage all over steel members.
What is the difference between hot dipped galvanization and pre galvanized material?
Pre galvanized material does not provide the requisite thickness of galvanization and service life guarantee comparable with HDG and painting system. 4.Hot Dipped Galvanizing ensures complete coverage over steel surface, irrespective of it’s shape, geometry.
Who invented hot dip galvanization?
Subsequently in year 1836, a French civil engineer, inventor cum chemist, named as Stanislas Sorel patented a method of galvanization by cleaning steel and then coating it with zinc by dipping it into molten zinc. This was the beginning of modern hot-dip galvanizing.
Is hot dipped galvanization sustainable?
2.Hot Dipped Galvanization is almost maintenance free. Once it is done, there is no requirement of reapplication or recoating. Hot dipped Galvanization is very much sustainable. In case of pre galvanized material, after some service life the pre-galvanized material needs replacement and / or maintenance.
What is galvanized coating?
1.Galvanization is the process of applying a protective zinc coating to steel or iron to prevent corrosion. There may be various other ways of corrosion protection; however galvanized coating is one of the most durable forms of corrosion protection.
Related Contents
- Hot-dip galvanized photovoltaic bracket buyers
- Hot-dip galvanized bolt manufacturer photovoltaic bracket
- Application cases of flexible photovoltaic panels
- Hot-dip plastic photovoltaic bracket
- Application of haze meter in photovoltaic panels
- Hot dip galvanized fixed photovoltaic bracket customization
- Photovoltaic bracket equipment application scenario diagram
- Photovoltaic support steel plate thickness standard
- Photovoltaic bracket installation application form
- Specifications of galvanized lines for photovoltaic panels
- Photovoltaic aluminum magnesium manganese plate manufacturer
- Haidong galvanized embedded photovoltaic bracket